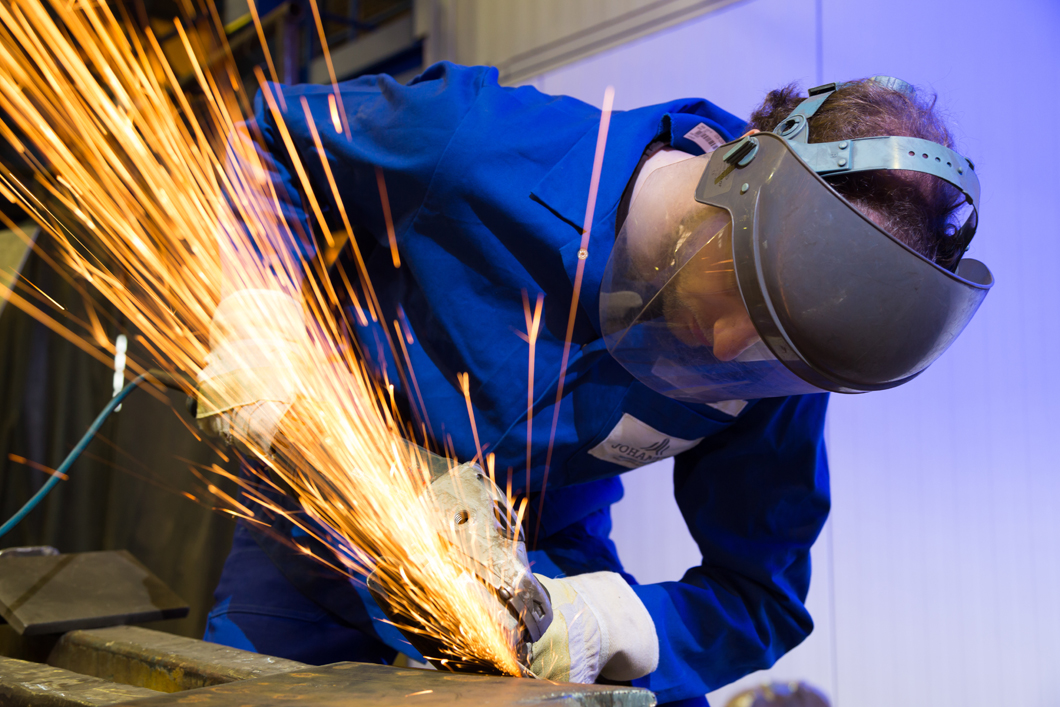
Business Owner Responsibilities Include Personal Protective Equipment
Nearly every occupation requires its workers to dress the part. Lawyers wear suits, doctors wear white coats and fast-food workers wear uniforms. But the more dangerous a job is, the more necessary the addition of personal protective equipment (PPE) becomes, and the responsibility to provide it falls solely on business owners.
Owner obligations
The Occupational Safety and Health Administration (OSHA) believes controlling a hazard at its source is the best way to protect workers. However, “when engineering, work practice and administrative controls are not feasible or do not offer sufficient protection,” PPE is the first-line of defense for workers, according to OSHA. Specifically, OSHA requires PPE to protect workers from injury or illness that stem from contact with chemical, radiological, physical, electrical, mechanical or other workplace hazards.
Since 2008, with a few exceptions, OSHA requires business owners to pay for PPE used to comply with OSHA standards. However, OSHA does not have requirements about what specific PPE business owners must provide.
According to OSHA, business owners must assess the workplace to identify and control physical and health hazards. They must identify and provide appropriate PPE for employees, train employees in PPE use and care and maintain PPE, including replacing worn or damaged clothing and equipment. They also should routinely review, update and evaluate the effectiveness of their PPE program.
OSHA does not require business owners pay for non-specialty safety-toe protective footwear (including steel-toe shoes or boots) and non-specialty prescription safety eyewear if the owner allows such items to be worn off the job site; everyday clothing, such as long-sleeve shirts, long pants, street shoes, and normal work boots; ordinary clothing, skin creams, or other items, used solely for protection from weather, such as winter coats, jackets, gloves, parkas, rubber boots, hats, raincoats, ordinary sunglasses, and sunscreen; hair nets and gloves worn by food workers for consumer safety; lifting belts; and when an employee has lost or intentionally damaged the PPE and it must be replaced.
PPE levels
Depending on the nature of an employee’s role and their job-specific tasks, different levels of PPE may be required. Under OSHA guidelines, PPE falls into four categories:
- Level A – To be selected when the greatest level of skin, respiratory, and eye protection is required. Level A PPE includes positive-pressure, full face-piece self-contained breathing apparatus (SCBA), or positive pressure supplied air respirator with escape SCBA, approved by the National Institute for Occupational Safety and Health (NIOSH); totally encapsulating chemical-protective suit; hard hat, coveralls and long underwear, when needed; chemical-resistant inner and outer gloves; chemical-resistant, steel toe and shank boots; and disposable protective suit, gloves and boots (depending on suit construction, may be worn over totally-encapsulating suit).
- Level B – When the highest level of respiratory protection is necessary but a lesser level of skin protection is needed. Level B PPE includes coveralls, disposable chemical-resistant outer boot covers, hard hat and face shield, when needed; positive-pressure, full-facepiece SCBA, or NIOSH-approved, positive-pressure supplied air respirator with escape SCBA; hooded, chemical-resistant clothing (overalls and long-sleeved jacket; coveralls; one or two-piece chemical-splash suit; disposable chemical-resistant overalls); chemical-resistant outer and inner gloves; and chemical-resistant steel toe and shank outer boots.
- Level C – When the concentration(s) and type(s) of airborne substance(s) is known and the criteria for using air purifying respirators are met. Level C PPE includes coveralls, chemical-resistant steel toe and shank outer boots, disposable chemical-resistant outer boot covers, hard hat, escape mask and face shield, when needed; NIOSH-approved full-face or half-mask air purifying respirators; hooded chemical-resistant clothing (overalls; two-piece chemical-splash suit; disposable chemical-resistant overalls); and inner and outer chemical-resistant gloves.
- Level D – For nuisance contamination only, work uniforms that offer minimal protection. Level D PPE includes gloves, hard hat, escape mask, face shield, safety glasses or chemical splash goggles, and disposable chemical-resistant outer boots; coveralls; and chemical-resistant steel toe and shank boots or shoes.
PPE protection types
OSHA classifies PPE under six protection types:
- Eye and face protection – OSHA requires business owners to make sure employees have appropriate eye or face protection if they are exposed to eye or face hazards from flying particles, molten metal, liquid chemicals, acids or caustic liquids, chemical gases or vapors, potentially infected material or potentially harmful light radiation. An eye and face safety equipment list should include safety glasses, goggles, welding shields, laser safety goggles and face shields.
- Head protection – OSHA says wearing a safety helmet or hard hat is one of the easiest ways to protect an employee’s head from injury. Hard hats can protect employees from impact and penetration hazards, electrical shock hazards and burn hazards. Hard hats must resist penetration by objects, absorb the shock of a blow, be water-resistant and slow burning and have clear instructions explaining proper adjustment and replacement of the suspension and headband. Hard hats must have a hard-outer shell and a shock-absorbing lining that incorporates a headband and straps that suspend the shell from 1 to 1 1/4 inches away from the head.
- Foot and leg protection – Employees who face possible foot or leg injuries from falling or rolling objects or from crushing or penetrating materials should wear protective footwear, according to OSHA. Also, employees whose work involves exposure to hot substances or corrosive or poisonous materials must have protective gear to cover exposed body parts, including legs and feet. If an employee’s feet may be exposed to electrical hazards, the employee should wear non-conductive footwear. PPE includes leggings, metatarsal guards, toe guards, foot/shin guards and safety shoes.
- Hand and arm protection – Employees must use protection if they face potential injury to hands and arms that cannot be eliminated through engineering and work practice controls. Potential hazards include skin absorption of harmful substances, chemical or thermal burns, electrical dangers, bruises, abrasions, cuts, punctures, fractures and amputations. PPE includes gloves, finger guards and arm coverings or elbow-length gloves.
- Body protection – Employees who face possible bodily injury of any kind that cannot be eliminated through engineering, work practice or administrative controls must wear appropriate body protection. Workplace hazards that could cause bodily injury include cuts; radiation; temperature extremes; hot splashes from molten metals and other hot liquids; potential impacts from tools, machinery and materials; and hazardous chemicals. Examples of body protection include laboratory coats, coveralls, vests, jackets, aprons, surgical gowns and full body suits.
- Hearing protection – Employee exposure to excessive noise depends upon the loudness of the noise as measured in decibels (dB), the duration of each employee’s exposure to the noise, whether employees move between work areas with different noise levels, and whether noise is generated from one or multiple sources. OSHA says the louder the noise, the shorter the exposure time before hearing protection is required. PPE includes single-use earplugs, pre-formed/molded earplugs or earmuffs.
The onus is on business owners to provide a safe workplace, including the personal protective equipment to prevent employee injuries and illnesses. Protective equipment is important because it keeps employees healthy and on the job, and business owners with safer workplaces can often benefit from lower workers’ compensation insurance premiums.
G & H Financial Insurance is committed to helping small businesses operate safer, more efficient workplaces. Contact G & H Financial Insurance today to learn more about workers compensation insurance at 281-395-5497.
Information Source: Employers