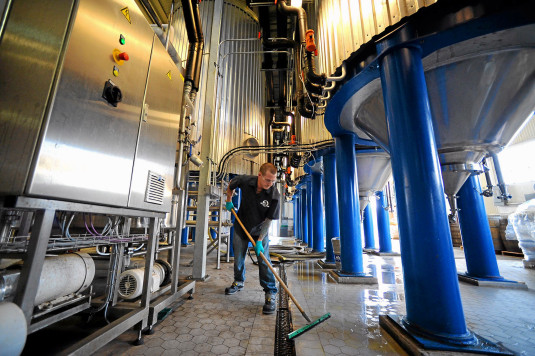
Brewing a Safety Culture in the Beer Business
Keeping up with America’s thirst for beer is hard work. In 2017, the U.S. beer industry sold 2.9 billion cases of suds, as brewers worked hard to keep up with demand. While Americans associate beer with good times, making the popular beverage is an exercise fraught with danger, which is why brewery safety should remain top-of-mind for mass manufacturers and small micro-brewers alike.
Beer brewing is a highly hazardous industry due to the use of hot liquids, pressurized tanks, caustic chemicals, fast-moving machinery, frequently wet floors and fork-lifts weaving in and out of the production floor, according to the Occupational Safety and Health Administration (OSHA). In 2016, breweries had a non-fatal injury rate of 4.4 per 100 employees, according to data from the U.S Bureau of Labor Statistics. As an industry employing approximately 60,000 employees, that’s around 2,700 injuries per year. Brewery management should be committed to creating a safety culture in the workplace for everyone.
What is safety culture? It’s about how people think, feel and interact in relation to safety. Companies that have a safety-first culture usually experience fewer employee injuries and greater productivity, teamwork and employee engagement. Creating a safety culture in the workplace is an ongoing process that requires commitment throughout the entire organization, from top management on down.
One of the most effective ways to design a safety culture is to make sure all employees, regardless of title or role, are aware of potential risks that exist in their work environment and the proper procedures that can prevent injuries from happening.
For breweries in particular, designing a safety culture is challenging, since there are unique hazards when compared to an office or other industrial setting. Commonly cited OSHA violations in breweries involve confined spaces, lockout/tagout procedures, hazard communication, fire prevention, forklift operations, personal protective equipment and hearing conservation issues, Craft Brewing Business and Occupational Health and Safety magazine both note. OSHA brewery regulations require breweries to develop specific programs to address all of these issues.
Here’s what you should know about each potential violation and the policies that should be in place to achieve a safety-first culture:
- Confined Spaces – Brewery workers often have to work in confined spaces, such as tanks, vessels or siloes. OSHA defines a confined space as an area large enough for a worker to enter bodily and complete work duties, that has limited or restricted entry and exit, and that is not designed for continuous worker occupancy. OSHA requires breweries to identify all confined spaces and then evaluate them to see if they require a permit for entry. If so, management must develop a permit system, train employees and create entry/rescue procedures.
- Lockout/Tagout Procedures – Breweries rely on a wide variety of equipment to make and distribute their beers. OSHA mandates lockout/tagout procedures for equipment maintenance and servicing where unexpected and hazardous energy could be released, such as a jammed conveyor belt or a steam valve that could suddenly release. Failure to control hazardous energy during maintenance activities can be serious, resulting in electrocution, burns, crushing, cuts, lacerations, amputations or fractures. In extreme cases, it can even be fatal. Brewery management must develop a written program that requires all energy sources to be identified and securely de-energized during maintenance work.
- Hazardous Chemicals – Like any modern manufacturer, breweries use hazardous chemicals in their day-to-day operations. To make sure workers use and store chemicals safely, OSHA requires employers to have a Hazard Communication Standard or “HAZCOM.” Management should develop a written HAZCOM program that includes an inventory of all hazardous chemicals in the brewery. Every container of hazardous chemical should be properly labeled or tagged, and sealed appropriately when not in use. Employees need to be trained how to handle and monitor chemicals, as well as perform regular maintenance of safety data sheets.
- Fire Prevention – OSHA requires breweries to have a written fire prevention plan for all facilities with more than 10 employees. The written program should list on-site fire hazards and designate which employees are responsible for maintaining fire control and prevention equipment. Emergency exits should be clearly marked and the pathways to those exits should be clear at all times. In the event of a fire, employees should know what steps to take to properly evacuate, or treat burns on-site, if needed.
- Forklift Operations – Beer has four basic ingredients: Grain, hops, yeast and water. These ingredients in bulk and other brewery materials are heavy, making powered industrial trucks, or forklifts, a common tool of the trade. According to OSHA, employers must make sure each powered industrial truck operator is competent and has completed training and evaluation. Forklift operator training should include formal (classroom) instruction, practical (on-the-job) instruction and evaluation of the operator’s abilities. Employees should also be trained in proper ergonomic lifting techniques for transporting smaller items around the brewery.
- Personal Protective Equipment – Whether cleaning tanks, bottling beer or boiling wort, brewery workers need to wear the correct personal protective equipment. The Brewers Association says this includes work-boots that protect employees from corrosive chemicals, hot fluids and physical injuries; clothes that cover the torso and extremities with material that can reduce injuries from thermal, chemical or physical hazards; eye protection to guard against injury from splashes, flying objects or poking; and task-based protective equipment, such as gloves and respiratory gear. Employers should assess the brewery to see where hazards exist that mandate the use of personal protective equipment. Then, they must select the appropriate equipment and provide training that includes when personal protective equipment is necessary, what equipment is needed, how to use the equipment properly, the equipment’s limitations, and proper equipment care and maintenance.
- Hearing Conservation Issues – Breweries can also be ear-piercingly loud places, so OSHA’s occupational noise exposure rules apply. Occupational noise levels within the brewery must be evaluated and addressed accordingly. OSHA requires employers to have a hearing conservation program in place if workers are exposed to a time-weighted average noise level of 85 decibels or higher over an 8-hour work shift. The program must include noise monitoring, employee training and periodic hearing exams. Employers also have to provide protective hearing devices like ear plugs or muffs in certain high-risk environments.
Brewery safety is a team effort. Management is responsible for ongoing hazard assessments, making sure workers follow standard operating procedures and providing the right training and equipment. Workers bear the responsibility to obey safety regulations, maintain clean workspaces, report hazards to management and use equipment and protective gear properly.
G & H Financial Insurance is committed to helping breweries operate safer, more efficient work places. Contact G & H Financial Insurance today to learn more about our cost-effective workers compensation insurance and brewery insurance at 281-395-5497.
Information provided by: Employers